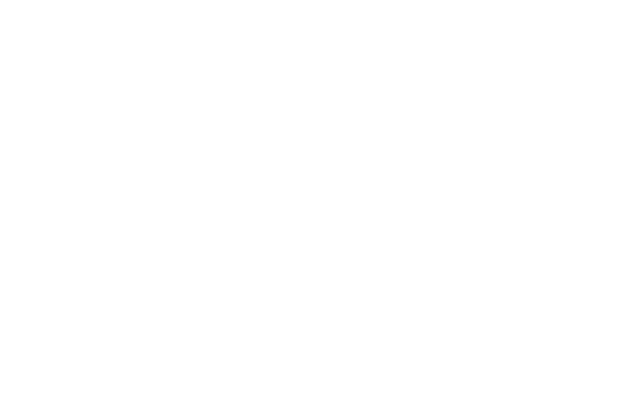
GTP is a premier custom injection molder in Northern Michigan for clients around the globe. GTP offers design, production, comprehensive in-house assembly services, including sub-assembly supply, line-side assembly, finishing, and sequenced kitting. This one-stop-shop approach streamlines the production process and ensures efficient delivery.
Precision Molding
Making injection molded plastics involves a few steps, each critical in its own way:
- Material Melting
- Injection into Mold
- Cooling Down
- Removing the Plastic Part
- Repeating the Process
In addition to these basic steps, GTP uses Scientific Injection Molding, a data-driven and systematic approach to the injection molding process. This method emphasizes using facts, measurements, and scientific principles to optimize every stage and achieve consistent, high-quality results with fewer defects at reduced costs. This approach is especially beneficial for complex parts, high-volume production runs, and applications where consistent quality is critical.
Taking this a step further, GTP also utilizes the RJG for process monitoring and the result include:
- Higher quality parts with fewer defects
- Reduced production costs
- Increased efficiency and productivity
- Minimized downtime and scrap
- Ability to make data-driven decisions for process optimization
Secondary Capabilities
GTP offers a variety of secondary capabilities to provide customers with added value, convenience, and efficiency. By offering a range of services beyond injection molding, GTP meets customers’ diverse needs, simplifying the manufacturing process, and enhancing overall customer satisfaction.
GTP’s secondary capabilities include:
- Finishing: GTP offers different finishing solutions, including ones to showcase an OEM's brand identity and provide valuable information directly on the injection molded part. GTP customers currently choose pad printing, hot stamping, and laser etching to brand their injection molded parts.
- Ultrasonic Welding: Ultrasonic welding is used to join plastic parts together without the need for adhesives or fasteners. GTP offers ultrasonic welding services to provide strong and reliable bonding between parts.
- Insert Molding: Insert molding involves placing metal or plastic inserts into the mold cavity before injection molding, resulting in a part with integrated inserts. This capability is offered to enhance part functionality and reduce assembly steps.
- Spin Welding: Spin welding is a cost-effective, efficient, and reliable method for joining plastic components in injection molding applications, offering benefits such as speed, uniformity, and hermetic sealing.
- Heat Staking: Heat staking is a versatile, cost-effective, and efficient method for joining plastic components in injection molding applications. GTP offers heat staking and the benefits include versatility, strength, and compatibility with automated assembly processes.
- Packaging and Fulfillment: GTP offers packaging and fulfillment services, where components are packaged according to customer specifications and handle shipping logistics. This is offered to provide customers with a complete solution from manufacturing to delivery.
These secondary capabilities are offered to provide customers with added value, convenience, and efficiency. By offering a range of services beyond injection molding, GTP can meet diverse customer needs, simplify the manufacturing process, and enhance overall customer satisfaction.